Energy Efficiency Between Light & Dark Panels
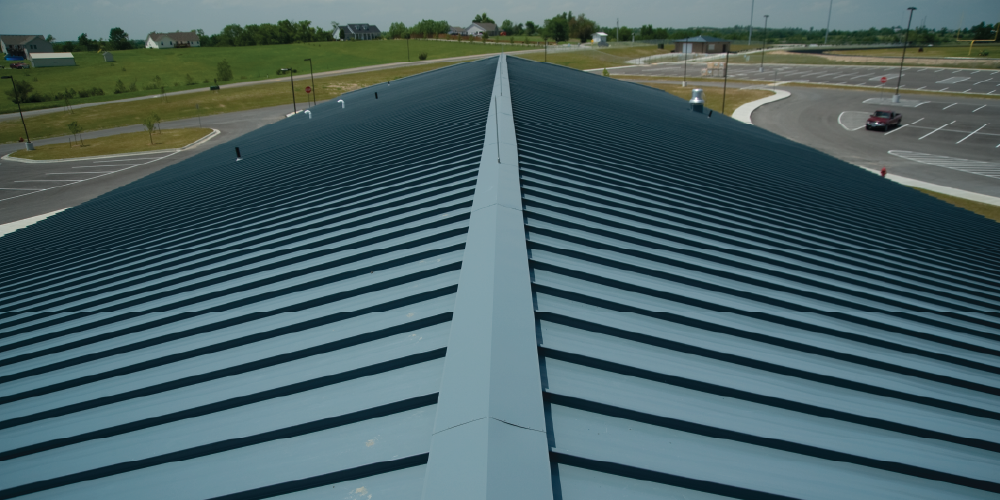
Making Earth-Friendly Choices A Priority In Construction
A recent press release from EY Canada, regarding the growing emphasis of Canadians on sustainability, announced that “…the majority of Canadians are pivoting to a more sustainable way of living, as over half are spending more time at home and focusing on saving their hard-earned dollars.” This applies to the desire for energy-efficient, eco-friendlier options when it comes to construction decisions, as well. And while that’s good news for the environment and the future for all of us, it doesn’t come without conflict. According to the release, “Most consumers (61%) plan to pay more attention to the environmental impact of what they consume, but 64% intend to focus on more value for money – creating a tension over who should pay for sustainability.”
As all of us in the construction industry look to find ways to offer customers greater energy efficient options without a lot of added cost, it’s good to know that technology is advancing along with demand, making it more convenient and simpler than ever before to make green construction a priority, not just a luxury.
Before any construction begins, a lot can be done simply by selecting the best building materials – especially the roof. The types of materials used make a significant difference in how well the building works with the environment to control temperatures and take the pressure off heating and cooling units. Additionally, colour choice can play an equally significant role in regulating the temperature. While darker exterior colours naturally absorb more energy from the sun, lighter colours work harder at reflecting both the light and its heat. Metal in general is naturally highly efficient at transmitting temperature – and making a smart colour choice that is suited for the climate in your area only enhances that effect.
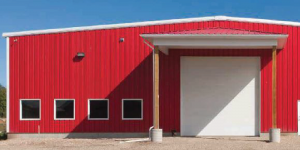
As a general rule, roofs with dark colours have been shown to absorb up to 90% of energy from solar rays. This translates into excess energy being transferred to your building’s interior, consequently causing air conditioning systems to work overtime. But a light-coloured roof can reflect, on average, 60% of sunlight and sometimes more – keeping your building cooler more efficiently. Additionally, the switch can result in average energy savings that can range from 7-15%. Cost and energy savings vary of course, depending on factors such as the size of the project, local climate, and how roof access is designed.
A lot of the energy-saving power of cool paint colours have to do with their makeup. Cool paint colours are made with cool paint pigments that have been chemically and physically altered to reflect infrared wavelengths while absorbing the same visible light. The pigments are designed specifically to minimize the build-up of excess heat. This process has also been shown to help mitigate Urban heat islands (UHIs) – a rising concern across Canada, due to the effects of climate change in addition to the growing number of Canadians now living in urban settings.
And in addition to all the benefits of cool colours on your metal roof, don’t forget that no matter the shade of paint you choose – your metal roof is always green. Exceptional energy efficiency is just one of the environmentally friendly benefits of metal building construction:
- Not only are metal roofs more durable and long-lasting, they are made from recycled content and can also be recycled once they do reach the end of their lifespan – creating a significant reduction in the amount of construction material that ends up in landfills.
- Metal roofs are easily compatible with solar panels, creating even more energy savings. With conventional roof systems, the expected lifespan of the roofing materials is often much shorter than that of the solar panels. Consequently, the panels must be removed while the roof is replaced and reinstalled once complete, resulting in added installation costs. But with the long lifespan of metal roofing, solar panels are unlikely to outlast them – therefore eliminating the need to remove and reinstall. And speaking of installation, it’s a much simpler process with metal panels. There are a variety of mounting options available that make it possible for the solar panels to be installed directly on the metal panels with no need to drill or create holes in the roof.
- Metal roofing is also a compatible fit for high-efficiency windows and skylights, offering easier installation and increased energy savings.
- The longevity and durability of a metal roof is nearly impossible to beat. With an average lifespan expectancy of 50 years or more and the ability to withstand extreme weather conditions, metal roofs require fewer repairs and replacements.
As the demand for construction that’s good for the earth and friendly for the budget continues to grow with Canadian consumers, you can trust Robertson Building Systems as your partner for quality materials that deliver on quality and stand apart in smart, energy efficient design.
The Builder is the Building Finding the Right Builder
Let’s talk about building. But let’s not talk about where, when or what you want to build. Makes sense, right? Actually, it makes more sense than you think. Stay with me.
The most important factor in making sure the where, when, what and how go smoothly is making sure you pick the right who. Because picking the right builder isn’t just another decision in the process – it’s the decision that will make or break the process altogether.
The right builder is the builder who is working long before any building begins. They are taking care of the less obvious, yet critical things like dirt work, plumbing, slab work, concrete, foundations, and all of the things that may never be seen but will definitely be noticed if not done well.
Finding the right builder
So now … how? How do you know when you’ve found the right one or how do you even begin the process of looking? Before you ever meet and shake hands with any prospective builder, there are several factors you can investigate to help you narrow down the choices.
- Look for a company with an established history. A company who wows you with their low prices or by being the new name in town may not be all they seem. Companies stay in business for many years and through multiple generations because they have earned a solid reputation and repeat business by treating people well and doing quality work.
- Talk to people. Talk to former and current clients of the builder. Talk to their suppliers and their subcontractors. These are the people who know the way the company does business and if they are fair and responsible. If they have not built a quality reputation with the majority of them, you have cause for concern.
- Determine if their capabilities and experience match your needs. Do they specialize in a specific type of construction? Or are they general contractors who do a little bit of everything? Depending on what you are building, the company’s project history and areas of expertise make a difference in the outcome.
Once you’ve narrowed down the best candidates, asking the right questions can help you further refine the decision making process. Every building is different, but in general, a lot of important details can be covered by simply discussing what you need the building to do for you: will you be using large equipment in the building? Do you need extra storage space? Refrigeration? Special consideration for stored products? Any details you can share with the builder will help streamline the process and avoid costly oversights.
Lastly, if you don’t currently have an option for financing, ask your prospective builder about it. Many builders can provide resources and guidance, which is a great added value for you.
Once you’ve gathered all of the facts and data and information, ask yourself a few questions: is this a person you like? Is this someone you could see yourself doing business with 10 years from now? Did you feel like their answers to your questions were honest and direct, even if not always exactly what you wanted to hear? Never underestimate the importance of just good old-fashioned human connection in matters of business. The most successful building and construction companies in the world will tell you – the most important thing you and your builder can build together is a trusted, long-term relationship.
Take the first step to becoming a Robertson Authorized Builder!
Become a Builder
A Growing Business: Metal Construction & Cannabis Cultivation
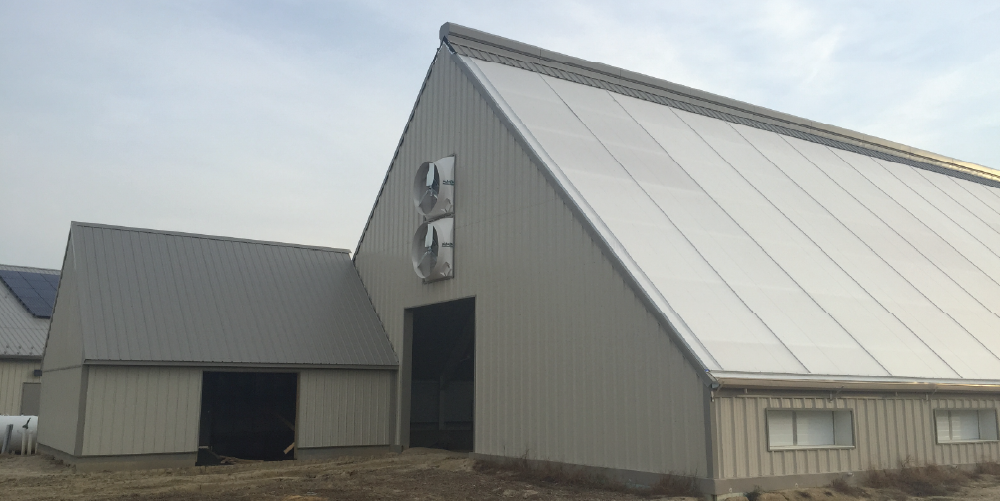
Canada was the second country in the world to formally and fully legalize cannabis, including its cultivation, possession, acquisition and consumption. Since it did so in 2018, the market has grown dramatically. Growth continued in 2019, when drinks, edibles and topicals were legalized. And even in 2020, a year plagued by the COVID-19 pandemic and related quarantines, Statista measured the Canadian cannabis market at $2.6 billion.
Straining to get Ahead
Cannabis is no longer an underground, black-market business. In fact, it’s very big business indeed. With demand suddenly through the roof, the medical and recreational cannabis industries are rushing to build new grow facilities and expand current ones just to keep up with a hungry market. However, even with the massively increased demand, cannabis is no commodity. Cultivators and cannabis entrepreneurs compete fiercely to develop stronger and stronger strains – or to unlock new balances of the compounds within strains to deliver a growing list of different desired effects. Across Canada, growers are looking to establish their competitive edge – or break through with new, better products.
A Highly Regulated Environment
Today’s cannabis cultivators are looking for an edge, and that edge begins with the environment in which the cannabis plants are grown. Cultivating market-busting cannabis requires absolute control of every environmental condition, so most growers choose indoor facilities, where a nearly tropical environment can be manufactured and maintained. Temperature needs to be controlled, regardless of whether it’s a muggy summer day or snow is piling up on the roof. Humidity and air movement also need to be precisely managed, giving enough moisture to plants without encouraging bacterial or mold growth. Powerful lighting and treated watering cycles are required to provide artificial seasonal cues to the plant, determining its phase of development and growing cycle – from seedling to growth to fruiting.
A Demanding Plant
All this management of temperature, humidity and air might seem like a lot, but it’s actually just scratching the surface. Each strain might require slightly different atmospheric conditions. Within a single grow facility, multiple different temperatures, varying levels of humidity and stages of growth likely exist next-door to each other to support the growth of different strains. This also requires extensive ceiling-mounted equipment, such as lighting systems, HVAC, MEP infrastructure, fire protection, mechanical, plumbing, electric, condensing units, watering systems and indoor blowers. All this ceiling-mounted equipment increases collateral load significantly.
As you can see, cannabis cultivation isn’t as simple as planting a seed. It demands much more of its structure than most industries. Luckily, Robertson’s vast experience in metal construction is ideally suited to outperform these demands – from structural requirements and performance characteristics to durability and cost. Let’s take a closer look.
The Perfect Match
Metal buildings – and the unrivaled features of insulated metal panel (IMP) construction, in particular – are the perfect match for cannabis cultivation. IMPs provide the entire building envelope, including the air, water and vapor barrier in a single product. IMP’s also have a built-in, foamed-in-place insulated core. So, instead of multiple trades installing multiple layers of the building envelope, a single trade can do it in a single step, reducing time, cost and exposure – and expediting dry-in times so interior trades can move in sooner. They not only withstand the consistent intense indoor humidity required in the cultivation process, but also extremes of cold, heat, rain and drought outside.
Imagine how long it would take multiple trades to install sheathing, water, air and vapor barriers, insulation and a rainscreen. Now factor in weather delays, scheduling errors and other problems. Compare that to IMP construction. Metal construction materials arrive on site pre-punched, drilled, and ready for assembly, reducing erection time by approximately 33% compared to other methods. A trained crew of four can install as many as 5,000 square feet of IMPs in a single eight-hour shift. That puts you much closer to your inaugural harvest.
Keeping Your Cool
The energy and environmental costs of running an indoor grow facility can be considerable, but with metal and IMP construction’s exceptional insulating properties and thermal uniformity, you’ll offset those costs by significantly reducing heating and cooling costs.
IMPs provide numerous other features, as well. Metal doesn’t support the growth of mold and is resistant to rust and decay, while creating a nearly airtight building envelope – keeping out pests, rodents, contaminants, and other intruders. Custom designed structures mean special drainage systems can be included, as well as recessed spaces in aisles for water faucets and easy-to-clean wall finishes – including specially formulated systems designed to stand up to routine, high-pressure washes. Metal construction is also perfectly suited to handle the increased collateral load cannabis cultivation requires.
Maximize Your Footprint
To enhance a grow operation’s profit margin, you need to make the most of every square foot of your building’s footprint. Robertson’s range of Primary Systems include Clear Span and Multi-Span framing options, allowing for column-free interiors and large, unobstructed, clear span space to support crops, water storage, processing facilities, product storage, and more. You can also explore the option of adding mezzanines and lofts to double the capacity of your building footprint. Furthermore, as your business grows, metal buildings can scale alongside, ready for a boost in demand to be matched by a boost in size.
Structures Tailored to Your Needs
Robertson metal buildings may commonly be called “pre-engineered,” but the truth is all components are custom-designed and made to order. When you contact a Robertson representative near you, we’ll consult with you about topographic conditions and site selection as well as both interior and exterior design. Your building will be custom engineered to meet both facility requirements and local building codes. When you trust your project to Robertson, you’re not only reducing the number of on-site trades and potential scheduling snafus, you’re also trusting a single source of responsibility. That means you know precisely what to expect – and precisely who to call should you ever encounter a problem.
Low Maintenance
Thanks to the unmatched speed of metal construction, your building will be erected before you know it. Once it is, the news gets even better, because it will be virtually maintenance free. Metal walls and sloped metal roofing are self-cleaning, requiring nearly no upkeep, which further reduces your operating costs. And your materials are backed by Robertson’s warranties.
Don’t let the others get ahead. Get in touch with a nearby Robertson representative today to start your cannabis cultivation project. The choice you make today could be the start of The Canadian cannabis industry’s next big name!
Robertson 2020 Photo Award Winners
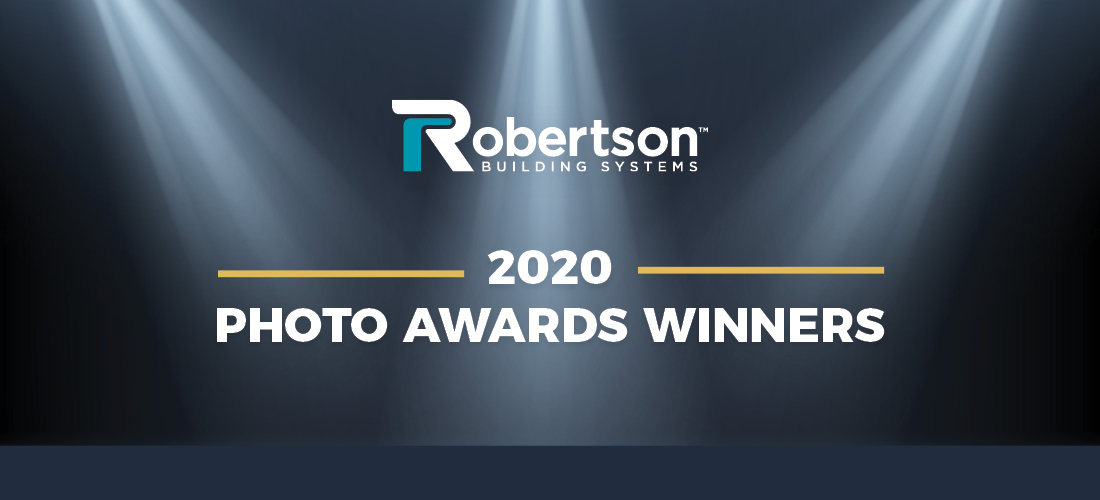
We are proud to announce Robertson’s 2020 Photo Award Winners! The quality of submissions continues to raise the bar for this competition and we are thrilled to see such design and innovation within our industry. Congratulations to all of our winners!
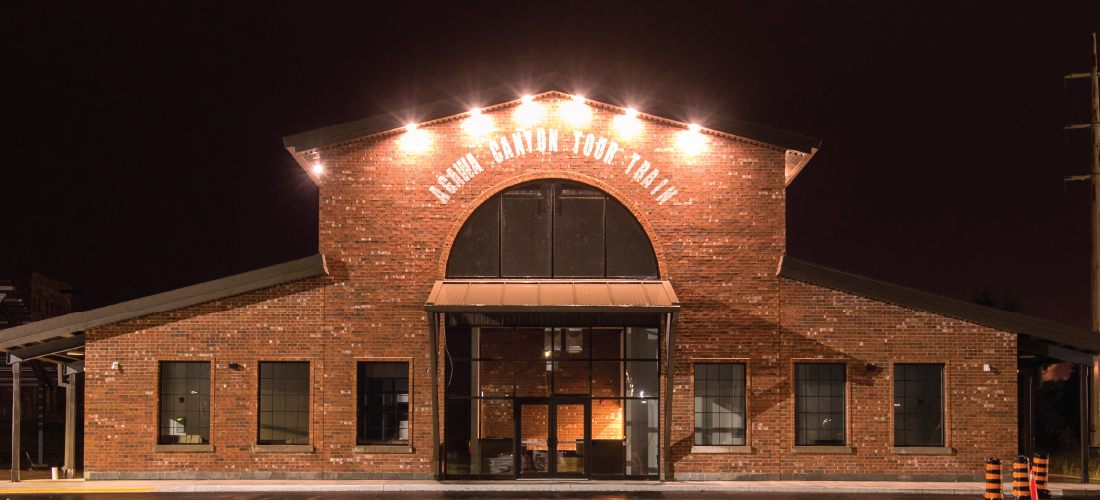
Robertson’s 2020 Building of the Year
The winning project is the Train Station by Superior Industrial Services in Sault Ste. Marie, Ontario.
This project is located in the Historical Canal District in Sault Ste Marie. The builder chose finishes that blend with the existing structures and incorporated repeating arched windows to mimic the original Gothic/Romanesque Revival style of the area as much as possible, while building on Robertson’s frame. This project is divided into four main areas. The first of which is The Train Station. There is a ticket desk, Employee offices and a waiting area for rainy days. The second area is an interactive gallery and retail space. The third area is a local craft 30 barrel brewery. The final space is home to a pub which seats over 100 people. Adjacent to these areas, is an outdoor rink with refrigeration that has its own Zamboni room and change rooms for the players to use.
- Framing: Multi-Span Building, Double-Slope with Straight Columns
- Total square footage: 20,918
- Building sizes:
- Building 1: 12,798 sq. ft.
- Building 2: 8,120 sq. ft.
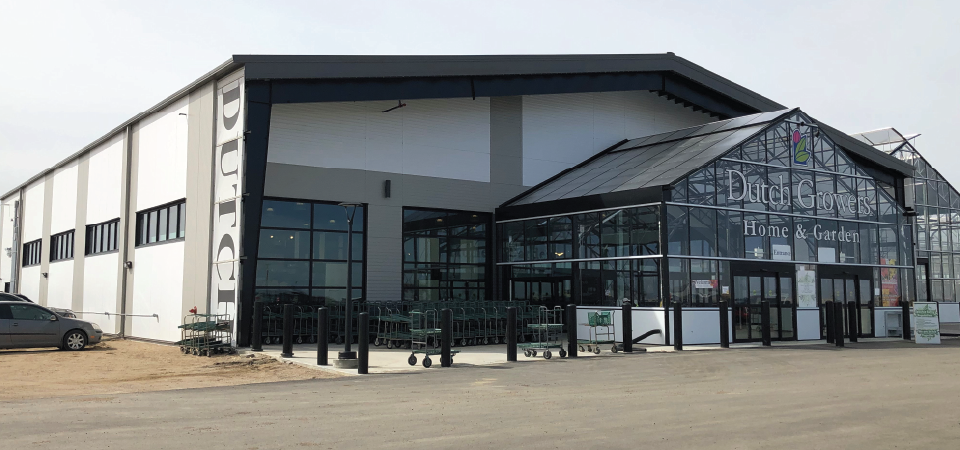
Agricultural Category Winner
The winning project is Dutch Growers New Garden Centre by Westridge Construction in Regina, Saskatchewan.
This two-building project is a commercial garden centre complete with greenhouses and a warehouse. The main retail area consists of a 24’ high building for retail sales along with offices and a mezzanine level. Previously this area of land was a golf driving range and the owners purchased the property in 2019 with design commencing in the fall of the same year and finalized it in the spring of 2020.
- The total square feet of this project is 14,010
- Framing: Clear Span Building, Double-Slope with Straight Columns
- Wall panel: CF Mesa Embossed in Solar White, Charcoal Gray and Ash Gray
- Roof panel: Double-Lok in Ash Gray
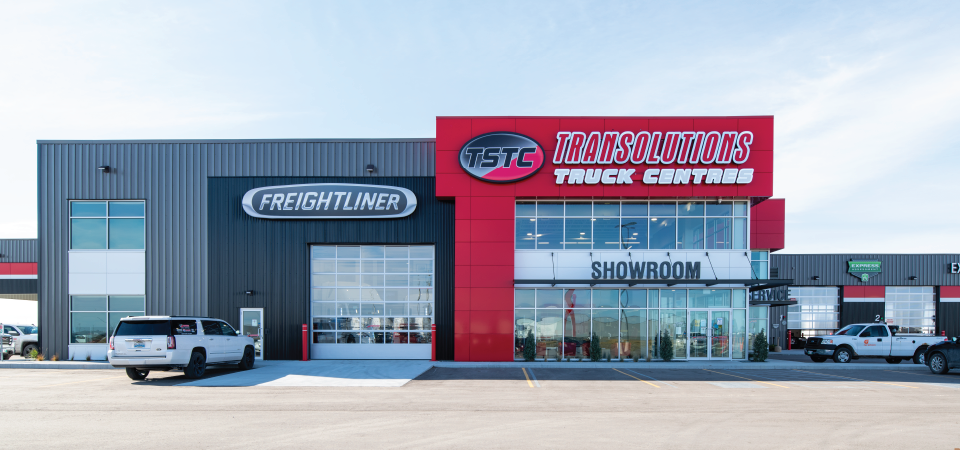
Automotive Category Winner
The winning project is TSTC Solution Truck Centre by Thomas Design Builders in Winnipeg, Manitoba.
This truck center is a state of art 82,000 square foot Freightliner dealership consisting of sales offices, express assessment, service shop, and parts. The project consists of three building and includes Pre-engineered buildings and an inverted pre-engineered structure with a conventional flat roof system. The building also has a 2nd floor structure provided by Robertson. ·
- Framing:
- Clear Span Building, Double-Slope with Straight Columns
- Multi-Span Building, Single-Slope with Straight Columns
- Wall panel: AVP and PBC in Charcoal Gray and Black
- Roof panel: Double-Lok and Galvalume
- Building sizes:
- Building 1: 31,440 sq. ft.
- Building 2: 12,155 sq. ft.
- Building 3: 10,500 sq. ft.
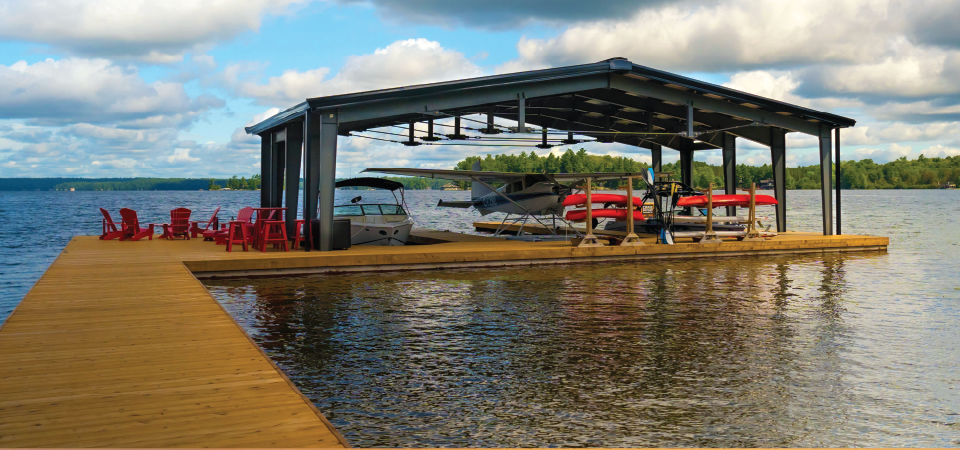
Aviation Category Winner
The winning project is the Dock Hangar by Kodiak Steel Buildings in Sarasota, Florida.
This winning aviation project is not your average hangar. It was built on Rock and Timber Cribs and is situated 150′ off the shore on the water. It was designed with additional rod bracing to reduce kick-out forces. This hangar was featured on the February issue of Our Home Magazine.due to its uniqueness. ·
- Total square footage is 2,200 sq ft.
- Framing: Clear Span Building, Double-Slope with Straight Columns
- Roof panel: Batten-Lok in Coal Black
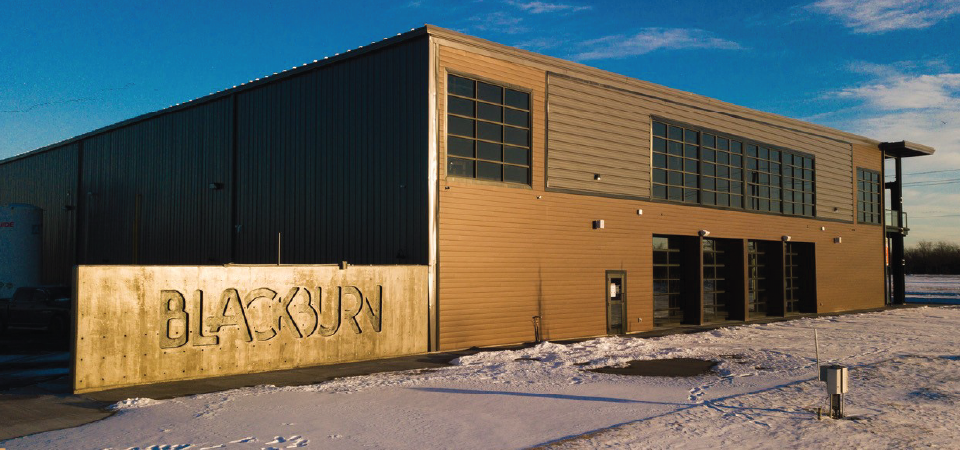
Commercial Category Winner
The winning project is Blackburn Brewhouse by Design Construct Solutions in St. Catharines, Ontario.
This project is an interesting mix of the craft brewing culture. This facility was built to be an experience and a brewing machine, with everything from interactive entertainment to dining, all while producing incredible amounts of contract beer brewing. ·
- Total square feet:
- Framing: Multi-Span Building, Single-Slope with Tapered Columns
- Wall panel: PBR in Charcoal
- Roof panel: Double-Lok in Galvalume
- Building sizes:
- Building 1: 7,200 sq. ft.
- Building 2: 21,600 sq. ft.
- Building 3: 4,800 sq. ft.
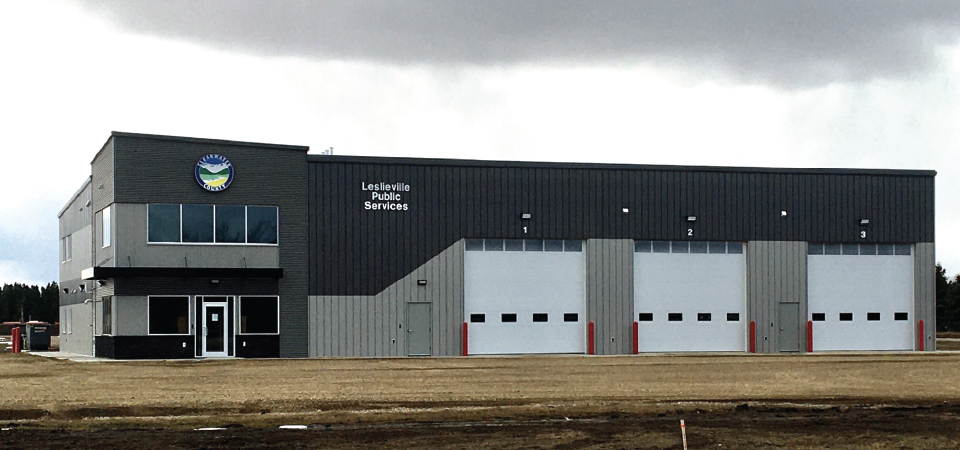
Government Category Winner
The winning project is Leslieville Public Services by Camdon Construction in Red Deer, Alberta, a combined fire hall and public works facility.
- Framing:
- Multi-Span Building, Single-Slope with Tapered Columns
- Multi-Span Building, Single-Slope with Straight Columns
- Wall panel: AVP in Ash Gray and Charcoal Gray
- Roof panel: Double-Lok in Galvalume Plus, with Robertson’s Thermal System
- Building size: 9,600 sq. ft.
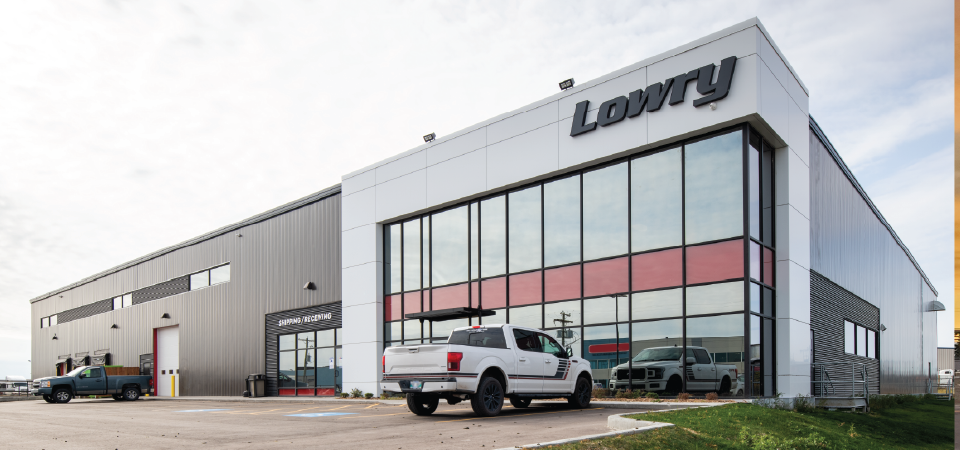
Manufacturing Category Winner
The winning project is Lowry Manufacturing by Thomas Design Builders in Winnipeg, Manitoba.
This is a 24,840 sq. ft. warehouse with a 3,000 sq. ft. office area. The building also has a 3,000 sq. ft. second floor mezzanine.
- Wall panel: FW-120, AVP, PBU and PBR in Charcoal Gray and Coal Black
- Roof panel: Double-Lok in Galvalume
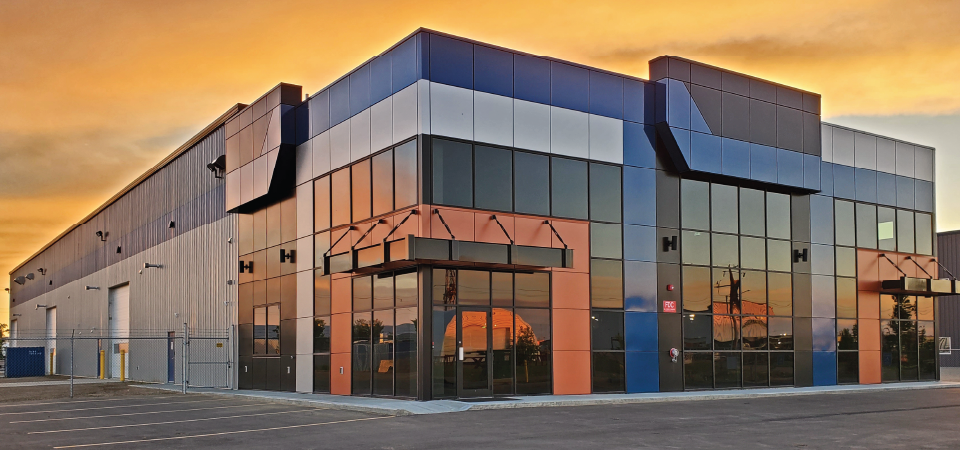
Office Category Winner
The winning project, a new manufacturing and office facility, is Rapid Design Group by Camdon Construction in Red Deer, Alberta.
- Total sq. ft.: 18,370
-
- Framing: Clear Span Building, Single-Slope with Tapered and Straight Columns
- Wall panel: AVP in Ash Gray
- Roof panel: Double-Lok in Galvalume
- Building sizes:
- Building 1: 15,750 sq. ft.
- Building 2: 2,800 sq. ft.
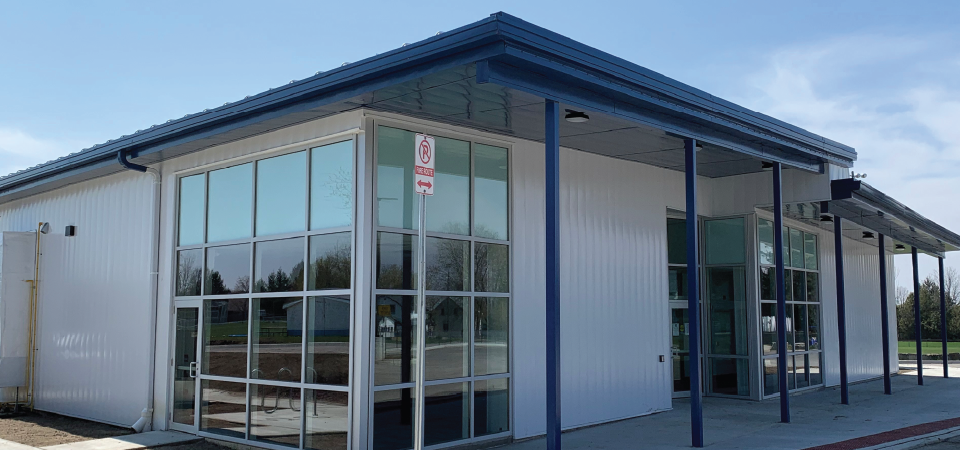
Recreation Category Winner
The winning project is the Thorndale Recreation Centre by MCI Design Build in London, Ontario.
This project is a community recreation facility complete with multi-use gymnasium, community meeting rooms, administration offices, storage areas, washrooms, change rooms and a kitchen. It is made up of 5 buildings for a total of 16,997 square feet.
- Framing: Clear Span Building, Single-Slope with Tapered Columns and a lean-to
- Wall panel: FW-120 and PBR in Solar White and Polar White
- Roof panel: Double-Lok in Galvalume Plus
- Building Sizes:
- Building 1: 7,438 sq. ft.
- Building 2: 4,242 sq. ft.
- Building 3: 2,100 sq. ft.
- Building 4: 1,723 sq. ft.
- Building 5: 1,495 sq. ft.
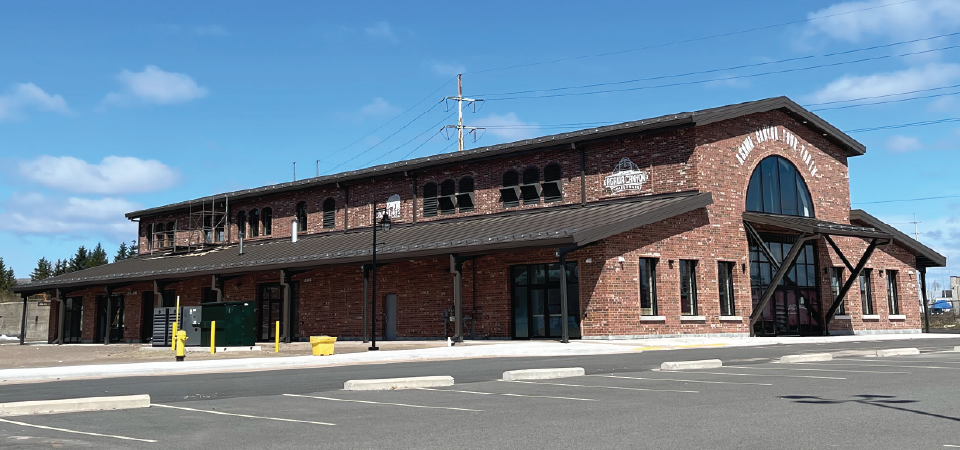
Retail & Restaurant Category Winner
The winning project is the Train Station by Superior Industrial Services in Sault Ste. Marie, Ontario. This project also won the 2020 Robertson Building of The Year.
- Framing: Multi-Span Building, Double-Slope with Straight Columns
- Total square footage: 20,918
- Building sizes:
- Building 1: 12,798 sq. ft.
- Building 2: 8,120 sq. ft.
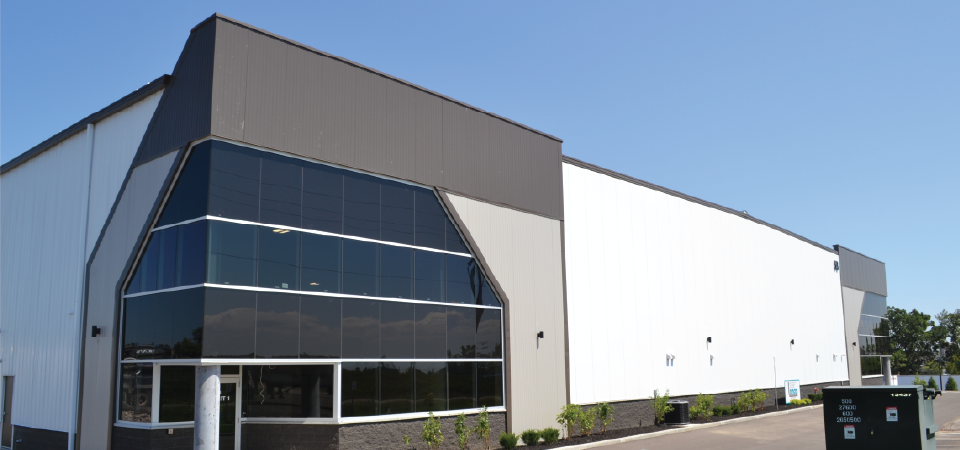
Storage Category Winner
The winning project is Euroline Appliance Warehouse by Lanca Contracting in Brantford, Ontario.
- Framing: Multi-Span Building, Double-Slope with Tapered Columns
- Wall panel: CF Mesa in Solar White, Burnished Slate and Ash Gray
- Roof panel: Standing seam roof in Galvalume Plus
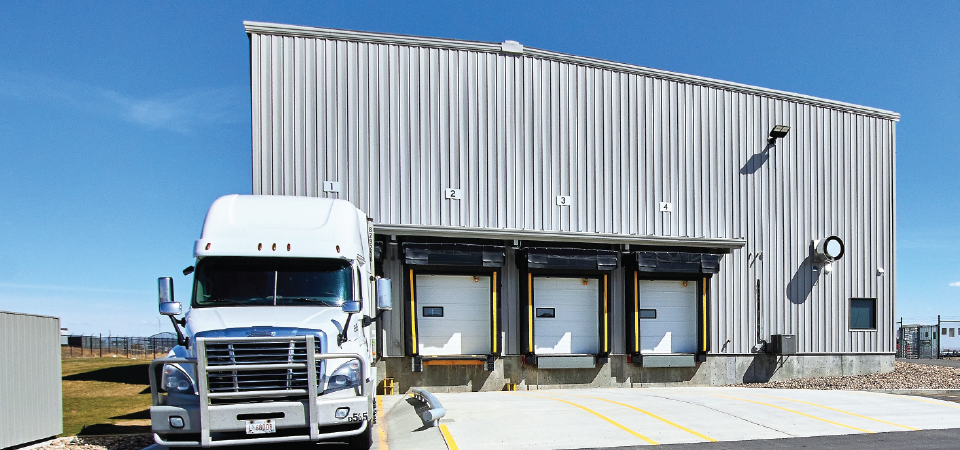
Warehouse and Distribution Category Winner
The winning project is FedEx Ground by Advance Design and Construction in Medicine Hat, Alberta.
This is a package shipping and receiving depot designed to accommodate a high quantity of shipping packages in a short order turn around.
- Framing: Clear Span Building, Double-Slope with Straight Columns
- Multi Span Building, Single-Slope with Tapered Columns
- Wall panel: AVP in Ash Gray
- Roof panel: Double-Lok in Galvalume Plus
Architects & Archetypes: Understanding the Roles of Architects and Engineers

Collaboration determines the success of any construction project. Dozens of different teams, specialists and tradesmen can be involved, each with their own concerns and responsibilities. It can sometimes be unclear who does what, who is responsible for what, and who should be involved at which point.
Today, we’re going to unfold these complicated connections, focusing on the roles of architect and engineer. We’ll also investigate cutting-edge methods to make projects go smoother, maximize profit margins, and minimize schedule changes by facilitating productive collaboration between architects, engineers and other stakeholders earlier in the process.
Who Does What?
You may be familiar with the notion of people being either more left- or right-brain dominant. If so, you have a good grasp on the fundamental difference between the characteristics and responsibilities of architects as opposed to engineers. Left brain dominance is associated with thinking, analytical processing, math, logic, and science, while right brain dominance is more feeling, creative, artistic, and free flowing. Of course, no one is entirely one or the other, and exceptions exist, but architects tend to be more right-brained while engineers are more likely to be left-brained.
Right-Brain: The Architect’s Vision
Most projects begin when an architect meets with a client, striving to understand their needs, goals and ideas. The architect then grows this into a grand, artistic vision which addresses those needs while elegantly integrating form and function in a surprising, impressive, memorable way. This vision is typically expressed in the form of a full set of architectural drawings comprised of floor plans, roof plans, elevations, sections, and perspective drawings.
This, of course, requires a good amount of left brain work as well. He or she must design within local codes and municipal limits, be aware of safety regulations and remain current on both technical innovations and city laws.
Once the architect has dreamed up a stunning and potentially groundbreaking building, it all exists on paper. But that doesn’t mean it’s constructible. That’s where engineers come in. Ideally, architects provide the following for an engineer’s review:
- Blueprints
- Floor-to-floor heights
- Slab edge locations
- Cavity depths
- Ceiling interstitial spaces
- Parapet locations and heights
- Unique architectural features
- Design areas subject to changes
Left-Brain: The Engineer’s Reality
Engineers tend to be the left-brained type, using math, science, logic, and visualization to fully understand the constructability and feasibility of an architect’s design. Using the architect’s preliminary drawings and the information listed above, an engineer designs a structure to support the building’s live, dead and environmental loads.
The engineer ensures the design is safe, meets building codes and specifies not only the structural materials and members, but details such as electrical, heating, ventilation, air conditioning and plumbing systems. On larger projects, each of these might have their own engineer assigned. Just as the architect provided information to the engineer, the engineer in turn provides the architect with crucial information:
- Structural implications of proposed openings and floor spans
- Size and locations of columns
- Locations and types of expansion joints
- Locations of shear walls or other seismic resistance mechanisms
- Possibilities for improving efficiency
Whole Brain: Collaboration
Until now, construction has mostly been a linear process: Plans move from a client meeting and resulting architect vision to an engineer review and construction itself. Today, though, technology is making it possible to streamline this in unprecedented ways. It can be hard to visualize all the places where a pipe might accidentally intersect a structural member or how columns might block the flow of hallway traffic when you’re working on paper or correlating various plans and drawings.
These coordination issues or “clashes” as they’re known, are now easier to predict than ever. The old way meant changes or unforeseen problems resulting in major problems in a project’s budget and timeline. Today, with the advanced software platforms and technology available, it’s possible to fully visualize a project before breaking ground – eliminating clashes before they become expensive problems.
The RBS Advantage
One of the biggest advantages for architects working with Robertson building projects is proprietary estimating software program, RBS. In the initial design and concept stages, architects can use the platform to present multiple design and pricing options to the entire team. With easy access to a wide variety of designs that incorporate all the necessary parameters and accessories, collaboration becomes much easier and architects, engineers, and the entire team can have the confidence of knowing the final design has maximum efficiency built right in.
When Architects & Engineers are Required
There are legal guidelines in place which dictate which projects need an architect’s involvement and sign-off versus those which can simply be reviewed and stamped by an engineer. Each province has its own Provincial Architectural Association with different requirements to practice.
Small, simple projects may not require the involvement of an architect or engineer. While many of the rules, laws and codes differ from state to state and municipality to municipality, the primary considerations are the classification of the building, its height and area. According to Part 9 of the Building Code, commercial project drafting work does not have to be completed by a professional. It is often performed by qualified technicians under the direction of the project engineer or architect. The structural design, on the other hand, will likely require direct involvement by an engineer. Check with your local permit office to be sure, but this gives a general of idea of what is required:
Requires Engineer Stamp
Single-story gas stations
Mechanic shops
Car washes
Small quick-service restaurants
Small single-story retail and office space
Requires Architect Stamp
Buildings over one story tall
Large or multi-story retail space
Large restaurants and offices
Big box stores, malls, etc.
Other instances in which an architect is certainly a wise choice is when repurposing a building designed for another use or when municipalities enforce more stringent design styles and materials.
Choose Wisely
Regardless of the size, scope and complexity of the project, the most important decision is choosing the right partner for you. Don’t let the sole decision-making factor be price. Your partner should be infinitely curious about your needs, goals, and concerns. They should be as enthusiastic and driven to realize your vision as you are. And they should be able to design and build within your budget.
If you have questions or concerns about finding the right architect, engineer or firm, get in touch with a Robertson representative near you. We have decades of experience working alongside architects and engineers with a wide spectrum of expertise and can help identify those who are most likely to best meet your unique needs.
Retrofit Buildings for Self-Storage
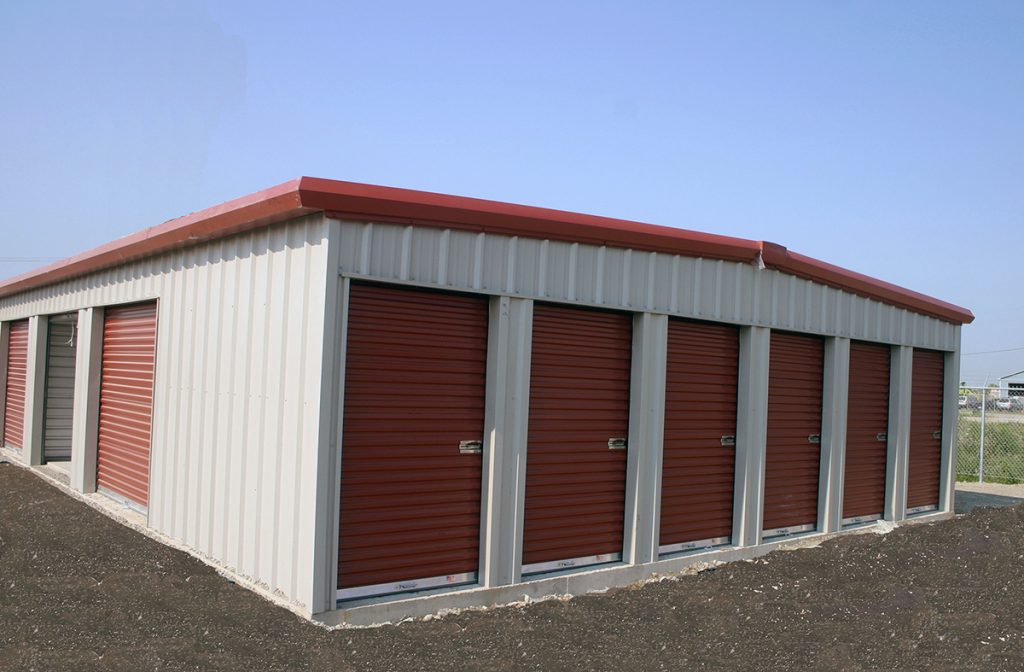
The Perfect (Retro) Fit
The self-storage business is booming in Canada. When the housing market goes bull, so does self-storage, and both have seen a healthy, steady incline – especially in urban and metropolitan areas. Even in more rural locales, self-storage is on the rise as “toy storage” for vacationers’ boats, RVs, ATVs and snowmobiles. Facilities are getting more expansive too. U-Lock Mini Storage Group president Robert Madsen explained in a recent Inside Self-Storage article that the 40,000-75,000 square foot facilities of yesterday have ballooned. “Today they can be 100,000, 250,000 or, in an extreme case, 500,000 square feet of net rentable space,” he said.
Locked Out
Demand may be up, but it isn’t all rosy for self-storage groundbreakers. There are several barriers to entry. Land costs are at an all-time high, and overall costs aren’t much better. As Madsen explains, “A modern, multi-story site ranges from $120 to $230 per square foot … far from the $55 to $70 of only a few short years ago.” Those are simply hard costs. There is also the much grayer, unpredictable prospect of rezoning. Apple Self Storage vice president David Allan points out “Rezoning is a much riskier process that has no outer time limit for completion… Even getting a site-plan agreement completed with the city of Toronto … take[s] 18 months.”
On top of that are Development Cost Charges, or DCCs. Paid by the developer, these are municipal taxes designed to offset the costs of continuing upgrades to things like local infrastructure, public transportation and social programs. But according to Allan, they’ve been reported to reach as high as $49.32 CAD per square foot – amounting to millions of dollars for the largest projects. These charges must be paid before construction begins. It’s all intended to be for the greater good, but as you can imagine, DCCs often stop a project in its tracks.
Robertson Has a Solution
There is a straightforward way to circumvent many of these barriers to entry. Land and construction costs can be offset by retrofitting an existing structure into a self-storage facility. A conversion project is much more cost-effective than buying, clearing, zoning and building from the ground up. As DBCI (sister brand of Robertson) Sales Representative Barry Nilson explains, “Because of the emergence of online sales, a lot of bricks and mortar, consumer outlets are no longer as popular.” That means across the country, you can find large, solid structures for sale in prime areas – ideal for converting into the self-storage that’s in such high demand.
Yesterday’s JC Penney, Kmart, gym, grocery store or even office and manufacturing space can be converted into self-storage. In fact, Walmart recently announced the closing of six stores in Alberta, Ontario, and Newfoundland.
Robertson specializes in providing a turnkey self-storage conversion project. From roll-up frames and door headers to modular wall and hallway systems, Robertson’s single-source, comprehensive, coordinated systems and depth of experience streamline the process from start to finish.
Due Diligence
At Robertson, we can handle quoting, delivery and speedy installation, but we highly recommend you attend to a couple items outside our area of expertise:
- Conduct a Feasibility Study
Before you invest substantial resources in a retrofit, consult the experts to learn about traffic in the immediate area, disposable income levels, competing self-storage facilities and expected community growth. Their findings can also help decide which unit mix is most appropriate. A college town full of apartments and dorms needs small lockers, while a sprawling, wealthy suburban area will rent larger units for furniture, heirlooms and even vehicles.
- Examine the Building’s Condition
A thorough inspection of your prospective property is essential to ensure it’s up to code, is structurally sound, has a solid roof and HVAC equipment in good condition.

Planning Ahead
Once you have your feasibility study in-hand, we can create an ideal blend of unit types and sizes, then design the floorplan to make the most of every square foot. If the building’s height allows for it, we can also consider the construction of a second-level mezzanine. Typically, at least 20’ of unimpeded height is needed for such a mezzanine, but it can essentially double your rentable space. Once a plan is approved and materials arrived, installation is typically fast and efficient – covering up to 8,000 square feet per week.
As a comprehensive manufacturer, supplier and installer, Robertson can also supply precisely what your future business needs to make it as modern and attractive as it is efficient and durable. With custom coatings, you can choose any color for your materials – including your precise brand colors. Furthermore, kick plates, corner guards, column wraps and wainscoting can protect your doors, walls and hallways from the scrapes, bumps and accidents that are all but inevitable in self-storage facilities. For lower clearance roofs, swing doors are an excellent choice. And to ensure the security of your tenants’ possessions, we offer burglar bars, mesh panels, and a selection of locks and latches.
It’s also smart to consider other value-added additions, like exterior updates to heighten your facility’s curb appeal and new restrooms. You could also include a small retail area for customers to buy essential supplies they may have forgotten or need, like cardboard boxes, tape, furniture blankets, stretch wrap, packing peanuts, dolly rentals and even pain relievers for tenants who might have overdone it.
Overhaul the Old U-Haul
Another trend sweeping the nation is renovation of older self-storage facilities. While they may not be much to look at, existing storage facilities do not face new construction challenges like land costs and zoning. With a contemporary facelift via clean new white Robertson metal panels, new doors, updated fencing and clean, bright LED lights, such a facility can feel like new. Robertson can streamline such an update too.
Ready to lock-in your project? Talk to a Robertson representative about tackling a conversion project today.
What Makes a Building Complex?
From Complex to Achievable: Foresight & Collaboration Make Complicated Structures Possible
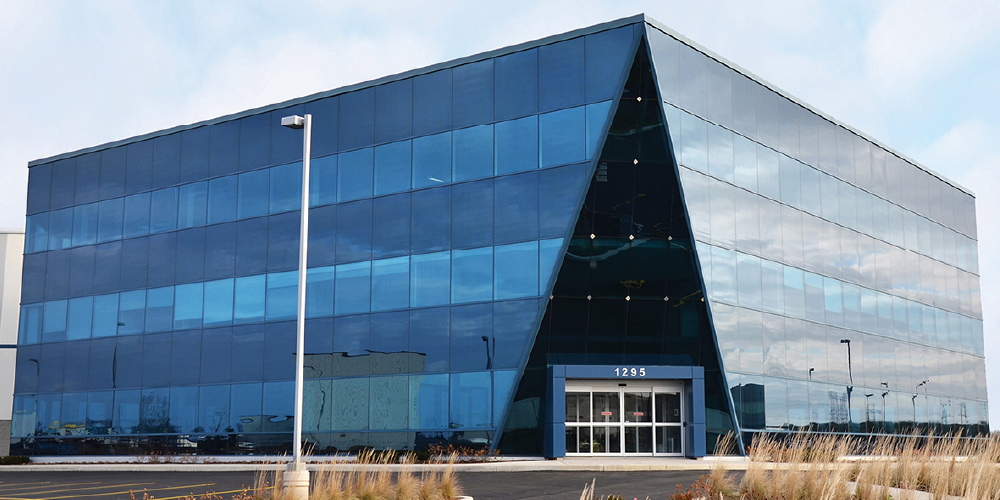
When you imagine metal construction, you might envision simple designs and basic construction. But with advances over the past few decades in every facet of metal construction, this is no longer the case. The capabilities and versatility of metal construction have improved drastically, pushing the boundaries of design and surpassing the expectations of architects, designers, builders and clients alike.
Once thought to be limited to the realm of conventional construction, relatively complex projects like retail establishments, car dealerships, schools and large sporting facilities are now being produced more quickly and efficiently using metal construction methods.
The Customer is Always Right
Understanding which building conditions result in a project being considered “complex” is the first step. The list below offers some guidance on these important qualities.
What Makes a Project “Complex”?
Understanding which building conditions result in a project being considered “complex” is the first step. The list below offers some guidance on these important qualities.
Examples of Complex Building Conditions:
A building with multiple roof hips and valleys one of the most common building conditions that lead to a building being considered complex.
Architects are usually involved to make a building more striking. However, the embellishments and complex geometries they envision can increase the intricacy of the engineering underlying the structure. This isn’t problematic – we simply need to collaborate, so all involved parties understand the vision and any limitations.
Whether it’s a second-level mezzanine or a basement, additional floors contribute to the complexity of a building.
Manufacturing facilities with structurally mounted equipment, such as large top-running cranes increase the design loading substantially.
Increased spacing between vertical supports is becoming an increasingly common building requirement – especially for indoor sporting facilities, warehouses and large churches. Clear span frames are used when unobstructed interior space is required.
Code changes and local differences for wind, seismic activity, snow, temperatures, energy and occupancy category may require more intricate engineering. Likewise, collateral loads for ceiling-mounted systems such as lights, ductwork and sprinklers can increase the complexity of the building.
Buildings constructed to house aircraft typically need very wide, high-fold doors for aircraft ingress and egress, requiring additional structural supports.
Metal construction is often chosen for its superior insulating values, and insulated metal panels further improve R-values. Daylighting is another efficient way to cut energy costs – bringing as much natural light in as possible. Though technology for including daylighting on a standing-seam roof has improved significantly, it still makes for a more complex design.
Collaboration
When your building meets the criteria for a complex building outlined above, the most important step you can take to save time and money is to involve your Robertson representative as early as possible. As Scott Schroer, Robertson’s Engineering Director explains, “Engaging with the architect, the owner, and our customer to help value engineer the building is a huge opportunity.”
Complex building conditions require custom solutions from our engineering department. Communication is key, because an engineer can spot problems or complications a builder, customer or even architect might not notice. They also have the experience and expertise to solve any issues that might come up.
Modelling Work
The inclusion of Robertson throughout the process also means we can take advantage of 3D Building Information Modeling (BIM). This software makes a visual model representing all the complex, interrelated parts of a building’s plan, from the framing and building envelope to mechanical, electrical and plumbing systems. By thinking proactively about complexities and where they might clash or interfere helps to avoid problems before they arise.
Metal construction can be more sophisticated and elegant than ever before – while still meeting and exceeding specific practical requirements. We just need to work together and communicate well. Contact your Robertson representative to get this important group conversation started as early as possible.
Air Quality in Buildings
A Breath of Fresh Air: How to Improve Indoor Air Quality
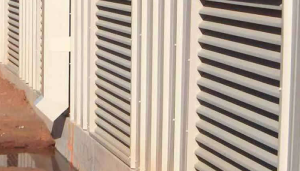
The Indoor Generation Report, a survey of Canadians conducted by The VELUX Group, revealed that though most of us don’t believe we spend too much time inside, most Canadians spend upwards of 90% of their time indoors. Between work, school, shopping and relaxing at home, the vast majority of our time is spent breathing stale, indoor air. Worse still, one in six Canadians lives in an unhealthy building.
As pandemic restrictions begin to lift and people across Canada head back to the office, return to school and venture back into indoor public spaces such as movie theaters, museums and retail establishments, indoor air quality is top of mind for all of us. But air quality isn’t a simple, single-variable concept. It’s a dynamic combination of many different factors. Fortunately, many of them are within your control.
The Impetus
Up until the 1970s, there weren’t strong and consistent regulations on building energy efficiency. This changed after a series of energy crises in the 70s and 80s which led to regulations which increased the thermal efficiency and air-infiltration of the building envelope. Thermal efficiency, as measured by r-value, is the insulation rating of a system, whether it is the wall, floor, ceiling, roof, etc. Air-infiltration, as measured by air leakage, is outside air that enters a building uncontrollably through cracks and openings.
Ever since, both the national and local codes have steadily increased the thermal efficiency and air-infiltration of the building envelope – especially in Canada’s northern climate zones. Beyond regulations, building tightness has been incentivized by the R-2000 Program and the EnerGuide Rating System from Natural Resources Canada. This has resulted in structures that are more and more airtight.
Competing Objectives
Thanks to these efforts, buildings have been able to maintain comfortable indoor temperatures better and more efficiently than ever. However, air tightness also means virtually no fresh air is allowed in, which can be detrimental to indoor air quality. Siet ‘Foeng’ Tjong, Robertson Head of Research and Development explains, “We generally do not like to have any leaks, whether it’s water, vapor or air leaks into the building. But in some cases that does create a problem with indoor air quality.”
We don’t often think of indoor air as necessarily being unhealthy, but it has the potential to harbor all kinds of harmful materials. As Joseph Dachowicz, Robertson’s Vice President of Marketing for Commercial Business, points out, “Buildings are filled with all kinds of man-made materials you’re just basically breathing in all day.”
Tjong agrees, “When you have a building that is super tight, it also creates a lot more challenges for the HVAC engineer to provide balanced indoor air quality,” she said, ”and it creates a lot more load and requirements on the HVAC system to evacuate the air inside building and replace it with fresh air.”
Pollutants
According to the Canadian Centre for Occupational Health and Safety (CCOHS), of the pollutants that can end up stuck inside airtight buildings, some are generated indoors, while others find their way in through cracks, open doors or windows, or even on the people going in and out. Some can come from both sources. But they all can become health and safety concerns.
Man-Made Volatile Organic Compounds (VOCs)
Chemicals used in the manufacture of office equipment, furniture, wall and floor coverings and construction materials can off-gas into your interior environments. Cleaning products, pest control, copying and printing can also leave variety of harmful compounds in the air. According to Health Canada, some of these VOCs, like benzene and formaldehyde, have been linked to cancer.
With extra cleaning measures in place due to COVID-19 concerns, and more sanitizing products being sprayed on more surfaces more often, ventilation to move that particulate matter out is even more crucial.
Biological Agents
Bacteria, viruses, fungi and moulds can all travel through the air, causing illness, infection and fungal or mould growth.
Combustion Pollutants
Whether from idling vehicles, machinery, tobacco smoke, heating or cooking, combustion-related compounds such as carbon monoxide are among the most dangerous interior pollutants. High levels of carbon monoxide from a vehicle left idling in a garage can be lethal in a matter of minutes. Worse still, it’s odorless, tasteless and colorless – virtually imperceptible without a carbon monoxide detector.
Fine particulate matter
This is the “dust” you can see floating in a ray of sunlight and can be made up of any of the above as well as other fine particulate matter.
Pollutants can be generated by the most innocuous seeming sources, such as housekeeping cleaners, air fresheners or printers, but are caused more precipitously by renovation, remodeling or applying new paint or finishes.
Health & Safety Effects
Poor indoor air quality can result in serious health effects. These can range from mild and irritating to life-threatening. Eye, nose and throat irritation are common, as well as headaches, dizziness and fatigue. At the more severe end of the spectrum, poor air quality can trigger asthma attacks, and more hazardous pollutants like radon or carbon monoxide can cause cancer or be lethal.
Sick Building Syndrome
When poor ventilation and indoor pollutants combine, they can lead to what’s known as “sick building syndrome.” Many occupants experience similar symptoms after entering in “sick” buildings, and their symptoms tend to resolve after leaving. Air quality this poor has been blamed for everything from sub-par student performance to reduced productivity in occupational settings.
Air Quality Perception is Reality
Individual perception of poor air quality is important as well. Though these considerations are more subjective, they can still affect how employees, visitors and customers feel inside your building. Odors and temperature are two of the strongest variables affecting perceived air quality, as well as air movement. Too little feels stuffy, but too much can feel drafty and uncomfortable.
The Basics of Air Exchange
Air exchange is a function of air infiltration, natural ventilation and mechanical ventilation. These each play a part in how much air needs to be exchanged or moved per minute, which is expressed in cubic feet per minute, or CFM. The more overall air exchanges per hour – including a measure of exchange with outside air – the better. However, the following factors and considerations contribute to what is required to manage and improve a building’s air quality and ventilation:
Size
The size of a building determines how much air is inside it, and therefore is an important part of the necessary CFM calculation.
Occupancy
Buildings with fewer or no people, such as barns or warehouses, require much less ventilation – fewer CFM – than buildings with higher occupancy, such as a school, office building or church.
Number and Type of Openings
These can be intentional openings such as doors, windows and loading docks, as well as a building’s unintended openings which compromise its overall tightness, such as cracks and broken seals. External pollutants infiltrate a building through such openings, then the building’s tightness keeps them in.
Type of Airflow
Unoccupied buildings may only have natural ventilation, while livestock buildings or storage buildings might use industrial fans, and buildings designed for people are equipped with complete HVAC systems.
External temperature changes
Outdoor temperature changes – both day/night cycle and seasonal changes – dictate what level of insulation is ideal.
Insulation Type and Quality
As discussed, insulation is good for energy efficiency but makes integration of fresh air a challenge.
Make Air Quality Part of the Plan
The absolute best way to ensure healthy air quality is to plan ahead and integrate adequate ventilation in your project from the very start. As Tjong points out, “Indoor air quality is the responsibility of HVAC engineers,” and they will be best enabled to provide that quality when their needs and input are included throughout the design process. Simply include HVAC engineers when you work with your Robertson representative. This way, fenestrations and other necessary roof and penetrations are planned for, as well as structural support for HVAC systems.
Under Your Control
We understand that while not everyone is undergoing a new construction design project, everyone can benefit from better air quality. Simply being aware of everything discussed so far will help you rectify any existing problems – and prevent future ones – while following these simple tips will help even more:
- Get healthy, fresh air into the building when possible.
- Establish an effective smoking policy that protects nonsmokers from secondhand smoke.
- Ensure your HVAC system’s HEPA filtration is changed as directed.
- Be careful not to place furniture or other obstacles in front of air vents, grilles or intakes.
- Water and maintain office plants properly to avoid extra moisture – and therefore the development of mould.
- Dispose of garbage promptly and properly.
- Pre- and post-occupancy flushing, with exterior air is recommended if your system is capable of it.
- Be mindful of the unintended consequences of excessive cleaning product usage.
Also, be wary of unsubstantiated claims of many air “purifiers” on the market that claim to kill COVID-19 or purify the air through unproven means. At best, these will be an expense that accomplishes nothing. At worst, they can exacerbate indoor pollutants. For instance, ionizers generate ozone. This is unhealthy on its own, but it’s also highly reactive and can combine with other airborne substances to create harmful VOCs like formaldehyde and acrolein.
There are steps everyone can take to improve air quality and incrementally improve the health of both buildings and the people who live, work, shop and play inside them. To learn more about how Robertson can assist in designing a custom metal building with the latest in air quality features, reach out to your Robertson representative today.
21 Trends to Watch in 2021
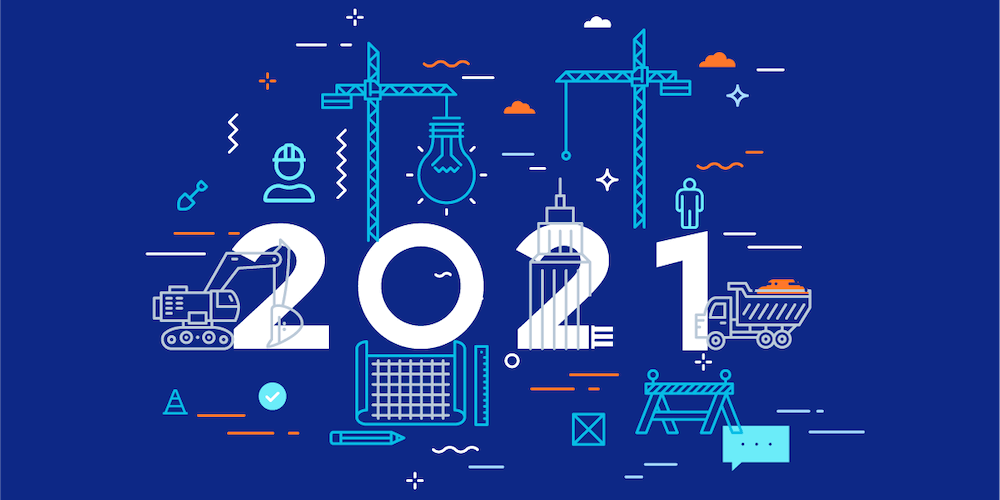
It is not surprising that an overwhelming majority of people around the world said they were ready to move quickly into 2021 and leave behind all the memories of 2020. The start of a new year, however, brings a desire to look forward to new, emerging opportunities. With this in mind, we have developed a compilation of some of the current trends in the construction industry and some of the technologies and tools that seem to be here to stay.
1. Green Building: The movement has become so popular that energy and environmental design (LEED) leadership now certifies nearly 2 million square feet of construction space worldwide. Commercial offices claim the bulk of the green building market, with just over 20%.
2. Modular construction: With a completion rate that can be 20-50% faster, lower construction costs, and a significant reduction in errors and waste, it’s not surprising that more builders choose modular construction. The optimized manufacturing processes used in modular construction also reduce the approximately 135 million tons of construction and demolition waste each year.
3. Autonomous machines: We’ve all heard that autonomous cars will be certain in the future, but what about automated machinery on construction sites? This is what happens – and at faster paces than those built for the road. Look for stand-alone machines to become even more common throughout the construction industry.
4. Device communication: It’s not just phones and computers in the office. Increasingly, small, and large construction equipment is being wired to interact and communicate, bringing efficiency to the maximum, improving safety, and streamlining costs.
5. Wider use of renewable biofuels: Construction professionals industry wide are abandoning diesel as a source of electrical equipment. This trend could significantly reduce the industry’s carbon footprint in the future.
6. Electric utility vehicles: Just by switching to battery-powered electrical machinery, the construction industry could reduce its emissions by up to 95%. Improved charging solutions that reduce downtime, which have been one of the biggest barriers to switching, making the transition easier for many businesses.
7. Drones: They are used to gain visibility into progress on construction sites and now used as a proactive method to identify potential problems before construction begins.
8. Cloud-based BIM: Moving building information modeling to a cloud platform rather than on-site makes information available to all stakeholders in real time. Communication is more effective throughout each construction phase, with increased response time and greater ability to respond quickly to urgent situations.
9. Dimensions plus BIM: As the technology moves toward 4D, 5D and even 6D capabilities, companies will be able to significantly improve estimation and planning processes through better data access. With the ability to see geothermal, thermal, and acoustic properties, builders can be more proactive in planning and even use information to determine how these properties will affect a building before construction begins.
10. Increased use of artificial intelligence (AI): A growing number of companies are joining AI in promising to increase efficiency throughout the construction process – from materials production to design, planning and implementation. There are also many opportunities to use AI to streamline the distribution process, simplify price forecasting and optimize the logistics of transporting a job – all factors in reducing the time and costs of a project.
11. Augmented and virtual reality: The main advantages of these technologies in the construction industry is the ability to identify weak points in a structure before allowing on-site workers to significantly improve safety and reduce accidents. In addition, with the use of remotely operated machines used from remote locations, work may continue when adverse weather conditions could otherwise stop productivity or increase the risk of accidents.
12. Collaboration through Business Information Modelling (BIM): A company that adopts BIM also improves communications at all levels. BIM allows teams to work seamlessly, no matter where they are: people in the office can communicate with those on the site and even with those in another city or country, not only by phone, email or text message, but in a graphic and interactive way. Improved communication helps reduce completion times and work costs while improving overall quality.
13. Smart Cities: Construction and engineering team planning planners are increasingly working with city leaders to turn cities into “smart” cities. A smart city has strategies to increase the sustainability of its communities and to ensure that these communities are built for resilience during difficult times.
14. Declining profitability: The least positive trends in the industry is a decrease in the profitability of construction projects. This change is due to several factors, including increased competition in Asia, increased project complexity and growing supply chain issues. To compensate for losses, many companies are working diligently to improve their project management processes.
15. Public and commercial facilities as leaders in green buildings: as industrial expansion increases, commercial buildings are at the forefront of green building initiatives. This trend is reflected in almost every region of the world, with manufacturers implementing innovative solutions such as green roofs, living walls, passive solar design, recycled and sustainable insulation, direct current (dc) power and plant-based materials.
16. Strengthening green buildings in China: In recent years, China has entered the leading role in sustainable construction with more than 300 million square metres of green buildings throughout the country. China is notoriously quick to adopt and implement green building initiatives – and is expected to have more than half of the world’s ground space for green buildings by 2021.
17. Increased use of 3D printing: At a time when construction workers are in short supply, 3D printing helps fill some of the gap by automating many of the tasks that are usually performed manually. The benefits, however, are not limited to supplementing the workforce. 3D printing uses only the materials needed to print a structure, virtually eliminating waste, and reducing costs. In addition, 3D printers can operate 24 hours a day, allowing faster turnaround times and turnaround times.
18. Shortage of hourly workers: With labour shortage in the industry that has continued over the past decade, construction companies are struggling daily to limit the number of projects they can take and to increase the time it takes to complete the projects they begin. In response, many companies are finding that they are increasingly dependent on prefabricated and modular materials, which require less practical time.
19. Employment in the construction sector is on the rise: As mentioned earlier, the lack of artisanal workers has led companies to work harder to recruit employees, including by offering higher rates of pay and more incentives.
20. Increase in regulatory prices: The number of building codes applied has increased by almost 10% in recent years, which has inevitably increased the cost of construction. Many professionals are convinced that new codes and changes are not necessary and do not lead to productive results, resulting in a general sense of frustration within the industry.
21. Increased awareness of worker safety: Increased regulations have also been incorporated in the areas of worker safety. As a result, more construction companies are implementing technologically smart tools such as portable trackers and even work boots with sensors. Devices allow supervisors to track the location of team members, let them know when workers are tired or injured, and much more.
Taking into consideration the information above, Robertson remains steadfast to meet the ever-changing needs of building erectors and contractors. To find out more about how to keep up with current trends and stay above the competition, contact your local Robertson representative.
Emerging 5G Technology is Set to Impact the Metal Building Industry
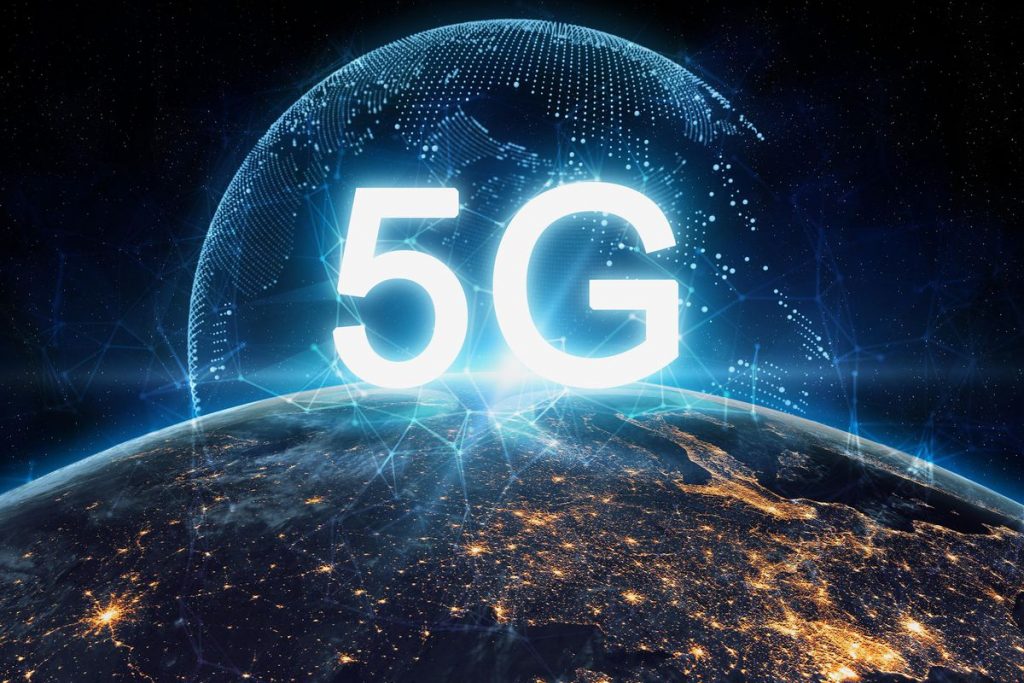
Construction companies of all sizes in every part of the country are using enhanced technology on job sites more frequently than ever. There are multiple benefits to making the investment, specifically in a video surveillance capacity: helping to reduce theft of equipment and materials, increasing the likelihood of identification if theft DOES occur, lowering insurance premiums, working to improve safety and reduce job-related accidents and injury, protecting against liability, providing clients with increased transparency and accountability on job progress, and more. And now, with 5G (fifth-generation) technology becoming more accessible to more people, the benefits for the construction industry are even greater.
With projected speeds of 10 to 100 times faster than current wireless technology and greater reliability, 5G capabilities will allow the construction industry as a whole to step into a more on-demand type of structure – enabling company owners and project managers to provide quicker responses, give customers greater peace of mind, improve communication between teams, minimize risk, and – in some situations – reduce the number of individuals needed on a job site. Specifically, in the metal building industry, 5G technology promises significant improvements in three key areas:
Manufacturing
With increased automation in the manufacture of metal building components in recent years, connection to reliable and efficient communication platforms is more critical than ever. Shifting away from dependency on wired ethernet connections allows greater efficiency and increased productivity with decreased need for square footage. Additionally, switching to wireless 5G technology enables more flexibility to move or rearrange equipment as needed, and gives manufacturers more options to automate certain operations and reduce the number of people needed for each step in the manufacturing process.
Design and Construction
Communication between teams is always a critical component to the success of a project – but when there are individuals in remote locations or who do not have reliable technology through which to share data or other information, delay and – worse – mistakes can occur. 5G can help bridge the gap by bringing all parties together on a common communication platform with the same network. Even in areas where Wi-Fi is not an option, 5G can keep teams connected through mobile access with real-time communication in virtually any location. Additionally, electronic tools such as stationary site cameras and drones can be connected to the 5G network and used to document, record and communicate on-site activity.
Completed Buildings
In today’s world of smart buildings, the demand for integrated technology in construction projects of all sizes shows no sign of slowing down. Consequently, increasing numbers of contractors and builders are seeking ways to incorporate 5G technology into construction plans. Building features can not only be customized to accommodate the specific needs of the client, but the flexibility of 5G also allows the manufacturer to collect data that can help improve their offerings to customers in the future.
As 5G technology and its game-changing speed and reliability moves closer to becoming the norm, the possibilities it holds for the metal building industry are virtually limitless. We are truly on the path to an entirely new definition of cutting edge – and your Robertson Building Systems representative would love to discuss new ways to make technology a solid part of your building plans.